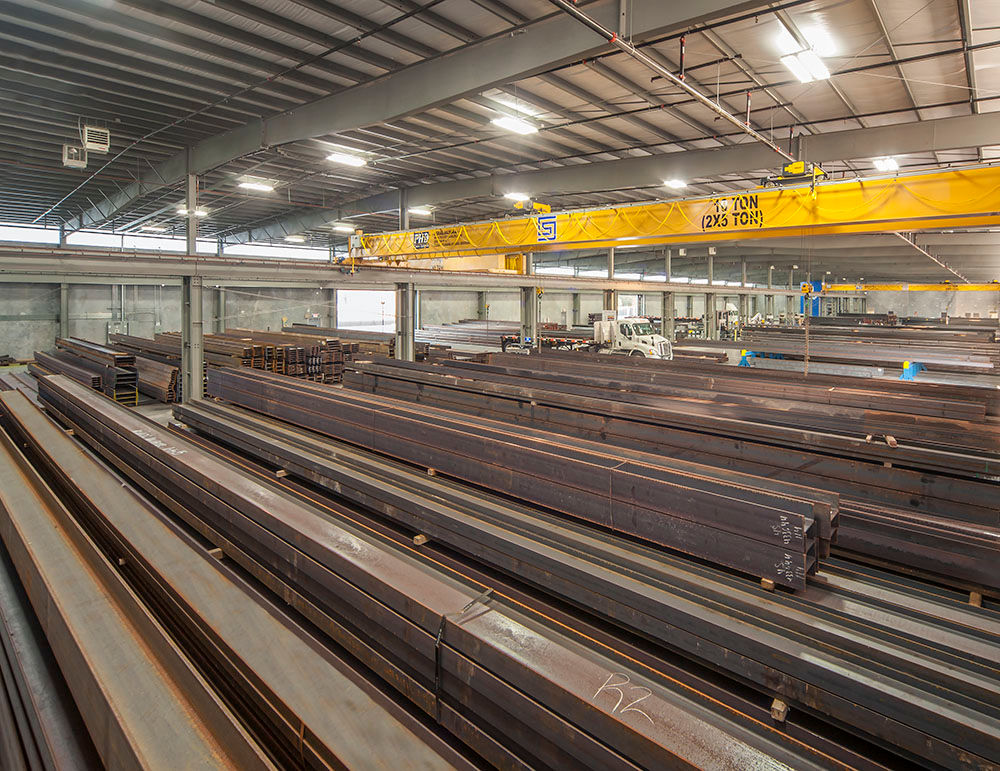
How Embed Plates are Made
Our Process
To make embed plates to your custom specs we start with plates of steel. The steel is loaded onto our plasma table which can easily accommodate plates 8' x 20 '. Each steel plate is cut into the embed plate size that you specify. This process gives us incredible control over both the size and shape of the plate. We can easily cut plates specifically for inside corners, long rectangles or simple squares.
Once the Embed plates are cut we use a stud welding gun to attach the studs to the plate. The stud gun generates an arc between the stud weld and the plate melting a bit of each. A spring in the stud welding gun activates pushing the plate and stud together, forcing the molten steel into a ceramic collar. Once the weld has cooled, the ceramic ferrule is broken off to reveal a perfect weld bead around each stud.
While studs can be welded by hand, the process is cumbersome and often yields inconsistent results. Using a stud welding gun ensures consistent high-quality welds every time- A must in critical structural applications.
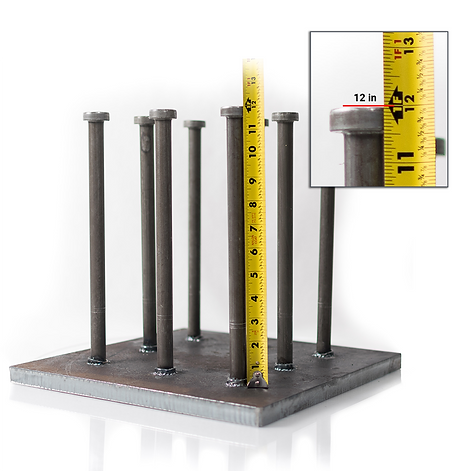

What makes stud welds so strong?
When the stud gun fires a number of things occur over the course of seconds to ensure the weld is super strong.
​
The stud gun creates an arc causing:
-
the aluminum tip to melt and clean the weld surfaces.
-
the steel plate and the stud weld to melt.
Then a spring in the stud gun activates, pushing the weld stud into the plate of steel.
The molten metal is displaced into the ferrule making the weld bead.
The weld cools and the metal of the stud and the plate are fully fused together.
The final stud height, as shown in the pictures, is 12".
The weld stud starts a bit longer than the final height of the stud. This extra metal is what creates the super strong weld between the stud and the plate.
The stud in the picture starts at 12 and 3/16"